EPS foam recycling - How to Recycle Expanded Polystyrene
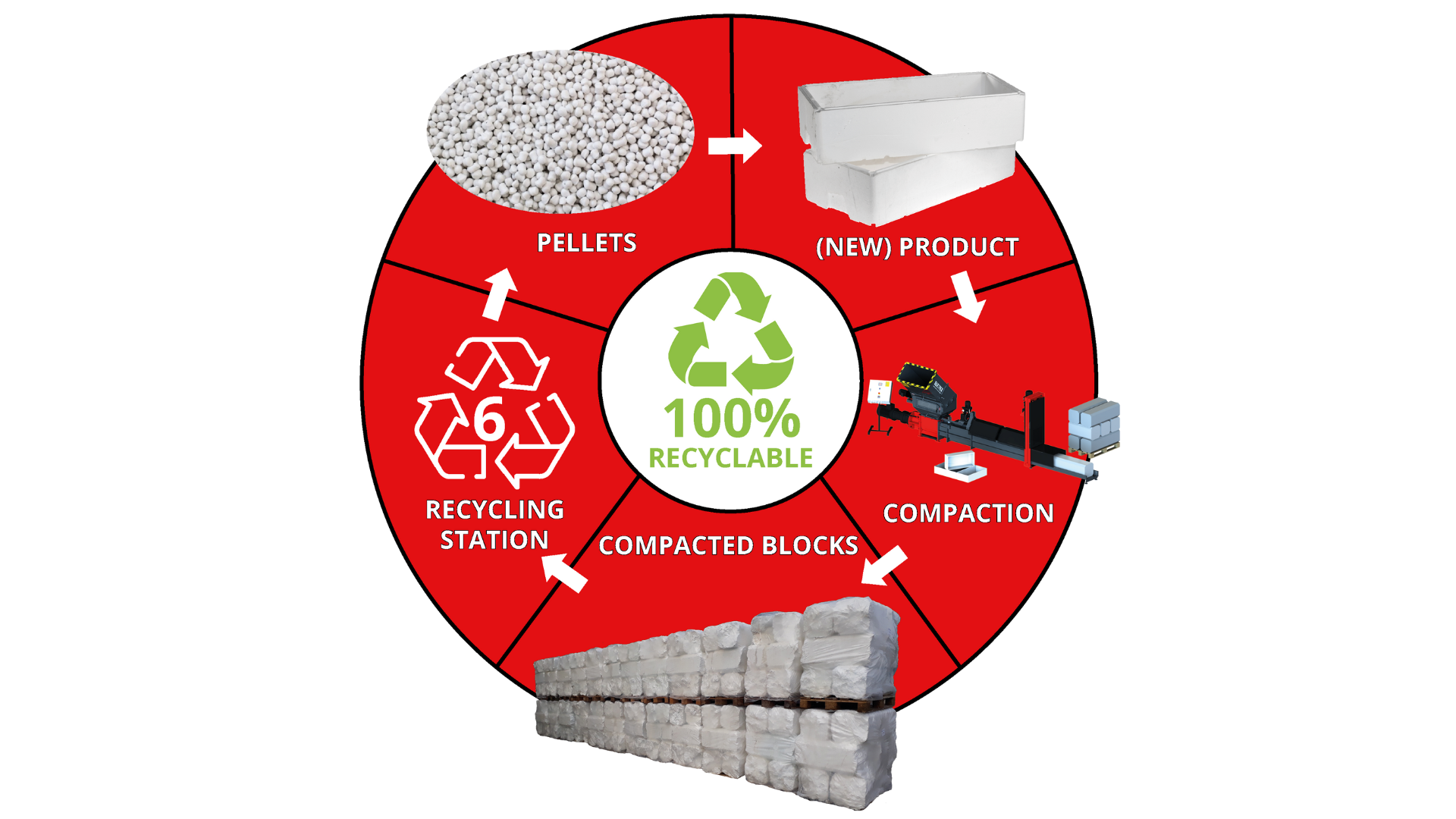
What Is EPS, And Why Is It Smart to Recycle the Material?
It goes by many names: EPS, styrofoam, expanded polystyrene, airpop and when you consider the many qualities of EPS it is no wonder that this material is widely used.
EPS is light-weight, durable, shock-absorbing, moisture-resistant and insulating and is therefore particularly suitable for protection of various products during transport and storage of e.g. food and medical equipment.
EPS is not biodegradable, but pure EPS is 100% recyclable. However, because EPS consists of 98% air, it can be expensive to recycle because it is very space consuming to store, just as it is expensive to transport once it has served its purpose. Therefore, EPS recycling in many places is deemed too troublesome and hence fully recyclable expanded polystyrene unfortunately ends up in landfills or incinerators in many places.
With RUNI's screw compactor storing and transporting EPS with 98% air is no longer an issue. In RUNI's screw press, the EPS can be compacted in a ratio of 50:1. In addition to making storage and transport cheaper and easier, the blocks of compressed EPS can be sold for further recycling and the demand for recycled EPS is increasing. For every kilo of EPS that is recycled, the use of 2 litres of oil is saved (The Danish EPS Association). EPS recycling thus provides both an economic and environmental benefit.
3 Steps for EPS Foam Recycling with RUNI Compactor
Step 1: Collect the waste
First, the EPS is collected separately and rid of other materials. This can take place in shops where EPS is sorted from other packaging materials or at recycling sites where the EPS is sorted from other types of waste. To ensure the highest possible price for the compacted EPS, EPS with concrete or dirt on it must be sorted out.
The pure EPS is then collected and shipped to the RUNI compactor. It is most optimal if the compaction takes place near the collection area, to avoid transporting large volumes of air with your pure extract.
Step 2: Compaction in the RUNI screw press
The RUNI is then fed manually via a conveyor belt or from a silo. When the EPS enters the hopper on the RUNI, it is crushed into smaller pieces by the pre-crusher. These chunks of expanded polystyrene then fall into the screw. Subsequently, the screw and the hydraulic jaws ensure that the EPS is compressed into blocks that are easy to handle, stack, and transport. The RUNI does not add heat to the process; it is the friction in the EPS itself that creates heat to ensure cohesive blocks. As a result, the RUNI uses less energy than other devices for compacting EPS.
Step 3: Pack and ship the compacted EPS for further recycling
The compacted EPS exits the RUNI in blocks that measure from 120x120 mm up to 370x370 mm, depending on the size of the machine. To ease the handling of the bigger blocks, RUNI offers a block divider that cuts the blocks into lengths that fit a standard pallet and a crane for lifting. The blocks can also be cut up manually. The compacted blocks can be sold to an extrusion plant, where the blocks are granulated and remelted. After the EPS is remelted, it becomes a new polystyrene granulate, which can either be used as polystyrene or made into new recycled EPS.
Find the Right Compactor for Your EPS Recycling
The quantity of your EPS and manner of feeding determines the most appropriate compactor you can use for your EPS recycling to get optimal results.
RUNI offers EPS compactors in 4 basic sizes:
SK120: This model is available in manual and automatic versions. They both have a capacity of 18 kg/hour, making them well-suited for places that handle up to 10 tons of EPS annually, e.g., retail and small industrial enterprises. This model is typically fed manually. Read more here.
SK200: This model is also available in manual and automatic versions. Both versions have a capacity of 45 kg/hour, making them a perfect fit for places that handle between 10 and 30 tons per year. In addition, this model is also available in a TWIN version with a capacity of 90 kg/day. This model is recommended for an annual quantity of up to 50 tons. These models are typically fed manually. Read more about SK200 here and SK200Twin here.
SK240: This model has a capacity of 75 kg/hour. It can be fed manually in a 45-degree hopper or with a conveyor belt in a vertical hopper. It is recommended for places that handle between 30 and 50 tons annually. Read more about SK240 here.
SK370: This model has a capacity of 200 kg/hour. It can be fed manually in a 45-degree hopper or with a conveyor belt in a vertical hopper. The model is recommended for locations that handle over 50 tons per year. Read more about SK370 here.
If you need a larger compaction capacity, we also offer larger systems where several compactors are combined with an independent shredder and a silo for storing the granulated EPS before it goes into the compactors themselves. Read more about our silo solutions here.
Want to Recycle Other Waste Types? Find More Recycling Guides Here
Do you have other types of waste, that you would like to recycle? Take a look at our other recycling guides:
Recycling of:
Besides our machines for compacting we also offer solutions for dewatering of various packagings:
If you need any further information, or you have any questions about the RUNI machines, please fill out the form below. We will contact you as soon as possible.