PUR recycling - Learn How to Recycle Polyurethane Foam - RUNI
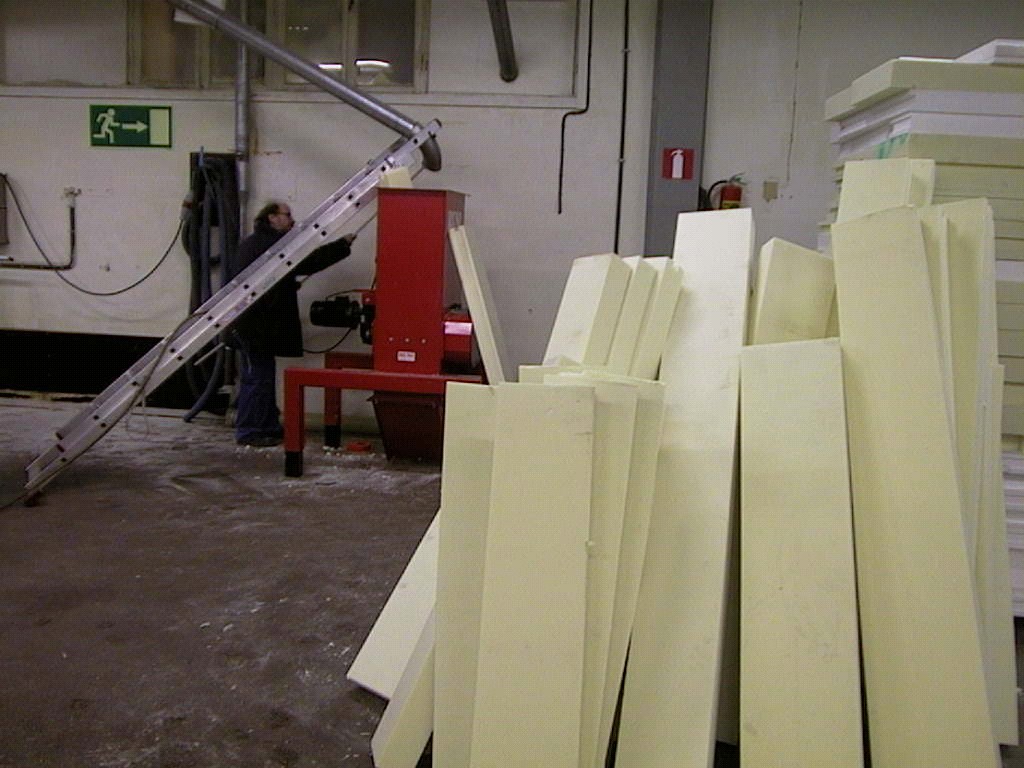
What is PUR (Polyurethane Foam)?
PUR is an abbreviation of Polyurethane. PUR comes in a rigid or flexible form.
The rigid PUR foam is very efficient as an insulation material for walls and panels in industrial buildings. It is used in insulated windows, cold stores, air barrier sealants, domestic appliances, and other industrial products.
The flexible PUR foam is found in bedding, mattresses, furniture, automobiles, carpet underlay, and a variety of consumer and commercial products.
How do you recycle PUR?
One essential question in today's global environment with the ever-increasing focus on a circular plastic economy is this: 'Is polyurethane recyclable?'
Traditionally, PUR ends up in landfills, but it is possible to recycle the PUR foam. It can be done by reusing the ground and reprocessing material in new products through chemical or mechanical recycling. The PUR foam can also be used for energy recovery, as it is a raw material that can be used as a replacement for virgin fossil fuel.
Chemical recycling of PUR is when PUR foam is broken down or dissolved in a chemical mixture like caustic solvents. After dissolving the PUR foam and processing the chemical mixture, it is possible to obtain a purified polyether.
Mechanical recycling of PUR is when the compacted and degassed foam is heated and made into new pellets that can produce new materials.
Energy recovery of used PUR is the last resort if recycling PUR is no longer possible. Then, the compacted plastic foam can be sent to incineration to create heating and/or electricity.
Step-by-step: Using RUNI PUR recycling equipment
When discussing recycling polyurethane foam, a significant concern is the logistics involved in the process. PUR, like all plastic foams, contains a great percentage of air, which makes it very hard to handle, sort, store, and transport. This is why compaction is essential when handling plastic foams. Furthermore, PUR foam also contains an explosive gas that can create dangers when this plastic foam is handled.
Step 1: Collect the waste
First, the material needs to be collected and sorted to ensure that all of the foam is PUR and that there are no nails/tape/wood pieces collected together with the PUR foam.
You can collect PUR in a manufacturing plant where off-cuts or faulty products can take up quite a lot of space and focus. In this case, it would make sense to gather as much PUR as possible and start compacting as soon as the material has been collected. It is always recommended to compact as close to the source as possible to save the cost of manual labor, handling, transport, and logistics.
Another place you can collect used PUR is a recycling station. Private individuals and companies can drop off their used PUR foams for recycling. It is equally advisable to compact your collected PUR as close to your source as possible, preferably next to the collection point. This is because it is very costly to transport the foam with air and gas inside.
Step 2: Compaction in the RUNI Screw press
When the collection of the PUR takes place, the recommendation is to put a RUNI PUR screw compactor right next to the collection point. Depending on the quantity of material to be collected in each place, a screw compactor is designed for the compaction of the PUR foam. The RUNI screw compactor for PUR has various extraction points inside its enclosed system. This is to ensure that the explosive gas is extracted and handled correctly. The RUNI compactor's extraction system is then connected to the company's or recycling station's extraction system.
When the foam is fed into the pre-crusher, it is shredded into smaller pieces, and some of the gas is extracted. The main gas extraction, however, takes place around the automatic jaws, which creates friction and compaction. The PUR screw compactor has a lot of easy-handling equipment, such as an automatic start/stop function, control box, and alarms to indicate if something needs adjusting. The process itself is continuous, and as long as there is material in the machine, everything keeps working automatically until there is no foam left to compact. The compacted PUR can then exit into endless bags that are easy and safe to handle and can be stacked on a pallet for transportation. This is a good solution, partially because the material can be toxic to get in close contact with and because the foam, when compacted, turns into a kind of heavy dust that is quite difficult to handle if not properly pushed into bags.
The compacting assures easy handling and makes the material take up a lot less space. After compaction, the PUR foam can be sold for further recycling. This solution for handling PUR foam is environmentally friendly as it uses very little electricity and helps this material stay valuable and ready for the next step in its life cycle. Overall, it is a more sustainable alternative to the traditional landfill or incineration options.
Step 3: Pack and ship the compacted PUR for further recycling
When the compacted PUR is gathered in endless bags, it eases further handling, such as transporting it. These bags are heavy and easily stackable on a pallet to ensure the maximum weight is achieved in the transporting truck. From both an economic and environmental point of view, it is always better to fill up the truck and use the maximum allowed weight than it is to transport foam, air, and a half-empty truck.
Take full control of PUR recycling with RUNI
What does the RUNI SK370 screw compactor for PUR offer?
- Handles up to 200 kg/hour (5 tons/day)
- Uses only 15 kw main motor (and 4 kw Heavy Duty Precrusher)
- Achieves up to 350 kg/m3 after compaction
- High safety levels
- Is CE-approved (can be ATEX-certified)
Learn how to recycle other material waste
Do you have other types of waste, that you would like to recycle? Take a look at our other recycling guides:
Recycling of:
Besides our machines for compacting, we also offer solutions for dewatering of various packaging:
If you need any further information, or you have any questions about the RUNI machines, please fill out the form below. We will contact you as soon as possible.