XPS recycling - How to Recycle Foam Board Insulation - RUNI
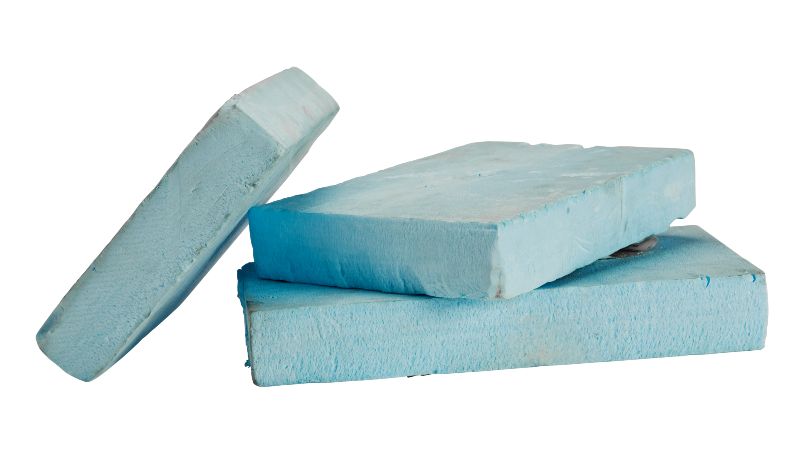
What is XPS?
XPS stands for Extruded Polystyrene. It is a lightweight cellular, rigid plastic foam or thermoplastic.
This material is widely used as insulation boards, especially within the construction industry. XPS is quite popular due to its outstanding resistance to water, temperature, pressure, and long-term reliability and durability.
Also, it is energy-efficient, easy to install, and easily recognized due to the well-known colors of the XPS foam sheets.
The density of XPS is generally between 25-45 kg/m3.
XPS Is Helping to Reduce, Reuse and Recycle
Extruded polystyrene foam insulation can help reduce energy loss in buildings, reducing the energy required to maintain a certain temperature in the house.
In other words - the more widespread the usage of XPS foam for insulating, the more we can save by reducing natural resources, such as oil, gas, or coal.
How Do You Recycle XPS?
Earlier, incineration and landfills were ways to dispose of XPS. However, XPS is not easily degradable by microorganisms due to its features (lightweight, large size, corrosion and age resistance, and chemical stability). Thus, these traditional ways are not recommendable. However, there are many good reasons to recycle the foam boards of XPS.
Used XPS can be recycled by melting and re-inserting it into the production of new extruded polystyrene foam insulation.
The manufacturing plants of XPS produce no waste XPS, as they are simply re-pelletized and introduced back into the production system.
The process of styrofoam insulation recycling starts after the product usage. When it has finished its function, the XPS is collected and compacted. Due to XPS insulation boards' high air content, it is costly to transport or store without compacting it first. Transporting without compacting first is also harmful to the environment.
Foam board recycling also helps mitigate landfill pollution, minimizing the potential threat to wildlife and the environment in general.
Besides the environmental advantages, efficient and dedicated waste handling is an essential thing for any company's reputation and ESG communication.
Summarily, recycling extruded polystyrene waste into new polystyrene products is the best waste-handling practice for any company handling this material. -It reduces the company's carbon footprint and gives XPS foam boards a new life as the same product or a renewed one.
Step-By-Step: Using RUNI XPS Recycling Equipment
The first step in styrofoam insulation recycling is collecting the material and, more specifically, the logistics of this collection. Like other plastic foams, XPS contains significant percentages of air, which makes the material very difficult to deal with in all aspects, including handling, sorting, storage, and transporting. Thus, COMPACTION is a keyword when handling this material.
Step 1: Collect the waste
Firstly, the material has to be collected and sorted. The XPS foam insulation boards mustn't contain nails/tape/wood pieces, or other things, as these cannot be a part of the recycling process.
The collection of used XPS foam could be in a recycling station, where companies and private persons can drop off their used XPS for this material to be recycled. To make the most of it, you can compact at this location to avoid transporting air, which is extremely expensive and unnecessary.
Another ideal place to collect extruded polystyrene for recycling is from XPS manufacturers with off-cuts or faulty XPS products that need compaction and recycling in-house or want to sell the compacted blocks for recycling.
Also, when looking for foam board recycling, turning to demolition companies for used XPS looks sensible, as we know that XPS is often used as insulation in buildings. Hence, materials can be found for compaction and recycling when buildings are torn down.
Step 2: Compaction in the RUNI Screw press
RUNI has developed an SK370 to handle the XPS, which, because of its structure, can be difficult to compact.
When the XPS is fed into the Heavy Duty pre-crusher, it is pre-crushed, and afterward, the screw and the automatic hydraulic jaws compact the material into uniform blocks. These can be stacked on a pallet for easy and efficient transport. The machine can be fed manually into a 45° hopper or with a conveyor belt into a vertical hopper. The incorporated sensors ensure easy operation with the automatic start and stop function. It is also possible to place the compactor under a silo for either XPS dust or smaller pieces.
Compacting ensures easy handling, and XPS takes up less space after being compacted. Compacted XPS in the form of blocks can be sold for further recycling.
The RUNI solution for handling XPS foam is very environmentally friendly. It uses very little electricity and helps the material stay valuable and ready for the next step in its life cycle. All in all, recycling with the RUNI solution is a great and sustainable alternative to the traditional landfill or incineration options.
Step 3: Pack and ship the compacted XPS for further recycling
Compacting XPS into stable and stackable blocks allows manufacturers to take advantage of the maximum weight allowed on a truck, ensuring they do not waste space and weight driving materials with air.
The blocks are very easy to handle and stack, but RUNI also offers a block divider for automatic separation of the block while exiting the compactor and a crane to lift the very heavy blocks and stack them correctly on the pallet.
Take full control of XPS recycling with RUNI
What does the RUNI SK370 screw compactor for XPS offer?
- Handles from 70- 200 kg/hour (depending on the density of the extruded polystyrene)
- Uses only 15 kw main motor (and 4 kw Heavy Duty Precrusher)
- Achieves up to 350 kg/m3 after compaction (10:1)
- High safety levels
- CE-approved
- Can be set up in an silo solution for even less handling.
- Block divider and crane are options for easy handling of the blocks
Learn How to Recycle Other Waste Material
Do you have other types of waste, that you would like to recycle? Take a look at our other recycling guides:
Recycling of:
Besides our machines for compacting, we also offer solutions for dewatering of various packaging:
If you need any further information, or you have any questions about the RUNI machines, please fill out the form below. We will contact you as soon as possible.